Industry 4.0 transforms chemical plants by integrating technologies like IoT, AI, and big data analytics to improve efficiency, safety, and sustainability. You can leverage real-time data and automation to optimize operations, reduce downtime, and minimize environmental impact. Strategic investments enable smarter decision-making, predictive maintenance, and eco-friendly practices. If you want to discover how these innovations are shaping the future of chemical manufacturing, you’ll find valuable insights ahead.
Key Takeaways
- Industry 4.0 leverages IoT, AI, and big data analytics to optimize chemical plant operations and enhance predictive maintenance.
- Digital transformation enables real-time process monitoring, resource efficiency, and improved safety through automated controls.
- Investments focus on integrating digital assets, risk mitigation, and developing new business models like value-added services.
- Technologies such as digital twins and blockchain improve sustainability, traceability, and supply chain transparency.
- Challenges include interoperability, cybersecurity, and high initial costs, but strategic adoption drives efficiency and long-term competitiveness.
The Core Technologies Driving Digital Transformation in Chemical Manufacturing
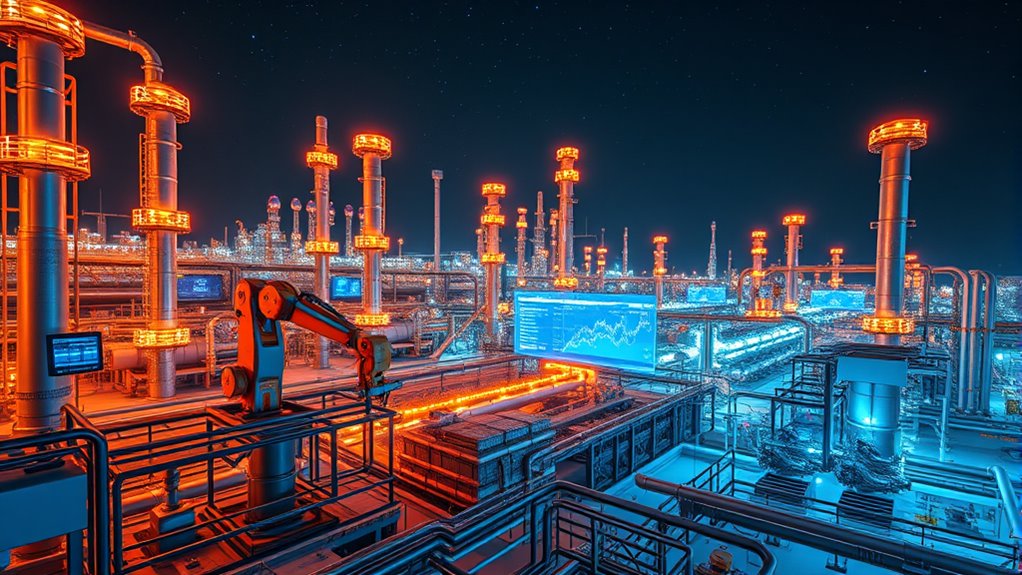
Digital transformation in chemical manufacturing relies on several core technologies that revolutionize how plants operate. IoT enables real-time monitoring through smart sensors, allowing you to track operational parameters continuously. It facilitates predictive maintenance by detecting equipment anomalies early, reducing downtime and maintenance costs. IoT also supports remote operations and automation, increasing flexibility and safety on the plant floor. The adoption of IoT is accelerating in the industry, driven by technological improvements and safety considerations. Machine-to-machine communication enables seamless process adjustments during production, improving product quality. Additionally, it helps embed smart features into products by collecting performance data from end-users, guiding future enhancements. Big data analytics processes vast sensor and operational data, optimizing efficiency and resource use. AI algorithms predict equipment failures and forecast demand, supporting decision-making. Cloud computing provides scalable storage and collaboration tools, accelerating digital transformation efforts across your plant. Emerging technologies are further enhancing these capabilities, helping companies stay competitive in a rapidly evolving industry.
Strategic Investment Trends and Growth Opportunities in Industry 4.0
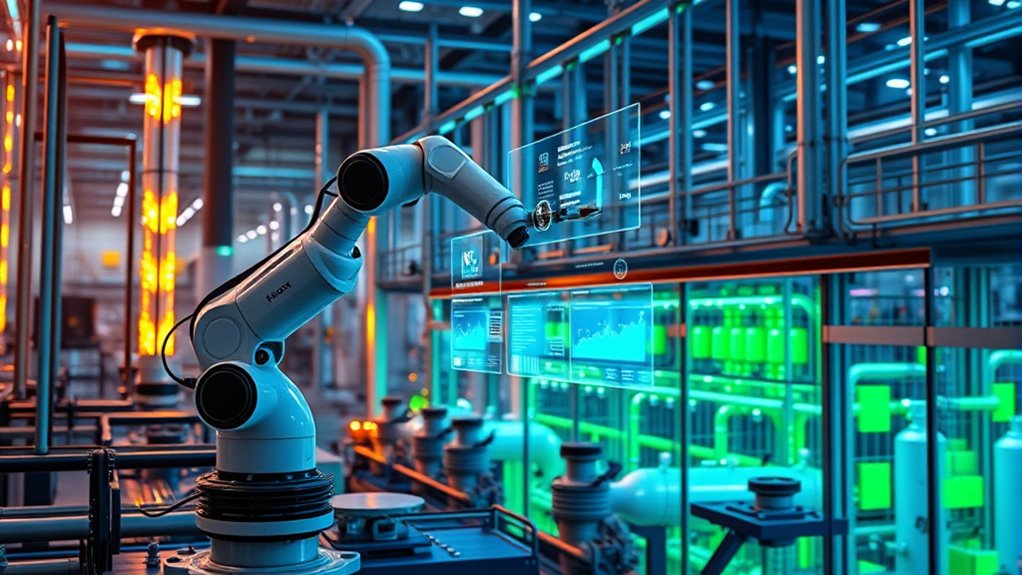
Investments in Industry 4.0 technologies are transforming the chemicals industry by boosting operational efficiency, enhancing risk management, and enabling new business models. You’ll see companies reallocating resources toward digital asset integration across value chains, which improves coordination and agility. Combines digital and physical advanced technologies to enable transformation. Strategic investments also focus on risk mitigation, ensuring compliance and reducing operational hazards. A key trend is shifting from traditional revenue models to value-added services and innovative products, opening new growth avenues. Market expansion is driven by developing advanced materials and smart chemical solutions. Additionally, companies are investing heavily in smart production lines, predictive maintenance, and data-driven decision-making, creating opportunities to reduce costs, improve productivity, and foster sustainability. The integration of digital technologies is crucial for staying competitive in the evolving landscape. These strategies position you to capitalize on the booming Industry 4.0 market, projected to reach USD 124 billion by 2030.
Enhancing Operational Efficiency Through Real-Time Data and Automation
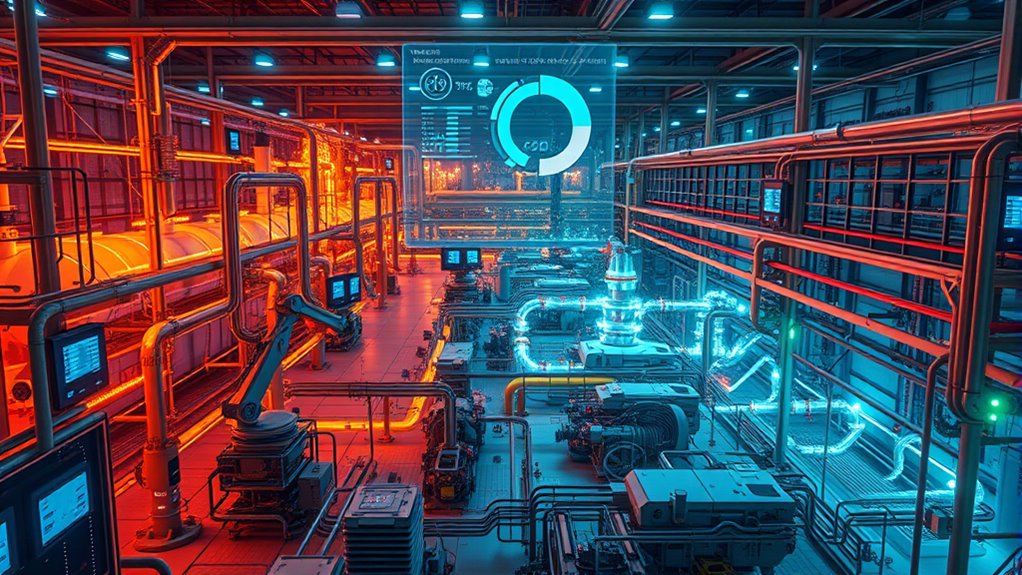
By leveraging real-time data and automation, chemical plants can considerably boost operational efficiency. IoT devices enable you to monitor process conditions continuously, providing instant insights into operations. Enhanced process controls and increased visibility through data and asset management allow for more precise adjustments and monitoring. Advanced analytics, including AI and big data, help you identify trends and make proactive decisions, reducing variability and optimizing workflows. Automated controls improve consistency and minimize human errors, ensuring safer, more reliable production. Predictive maintenance systems use AI to detect equipment issues early, reducing downtime and costly repairs. Automation of repetitive tasks frees your workforce to focus on strategic initiatives, while streamlined processes enhance product quality. Real-time data improves resource allocation, demand forecasting, and supply chain visibility, allowing you to respond swiftly to changing market needs. Additionally, understanding industry-specific operating hours helps optimize staffing and service levels, which is crucial for maintaining continuous production and customer satisfaction. This digital approach drives efficiency, lowers costs, and strengthens your competitive edge.
Sustainability Initiatives Enabled by Digital Solutions
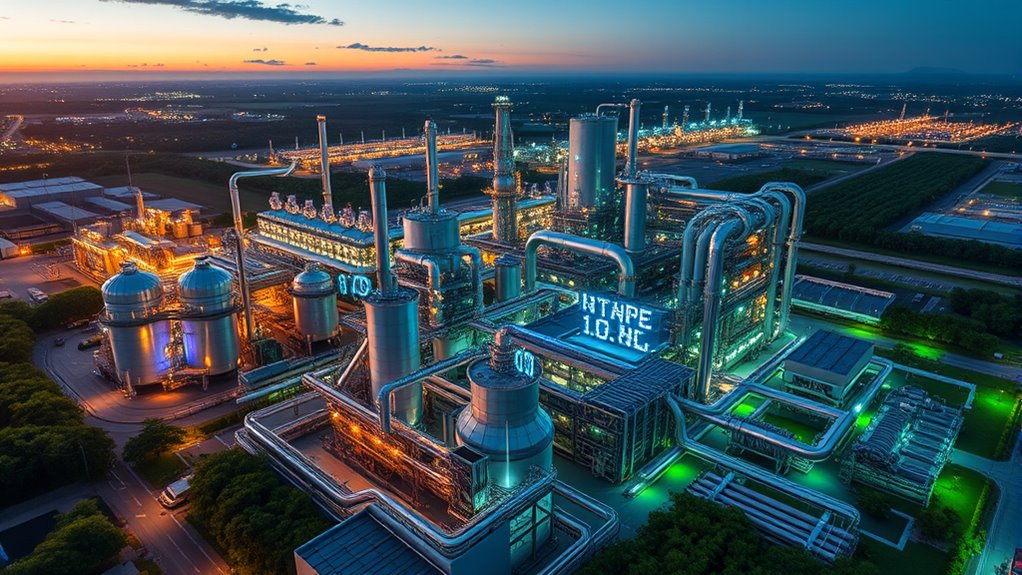
Sustainability initiatives in chemical plants are increasingly driven by advanced digital solutions that enhance transparency, efficiency, and compliance. Digital traceability and emissions monitoring enable you to track and audit emissions precisely, supporting your carbon neutrality goals. Incorporating cozy textiles and rustic decor elements can also foster a more inviting and sustainable workplace environment, emphasizing comfort and natural materials. Real-time data capture and verification guarantee transparent environmental compliance, while digital twins and IoT sensors help you simulate and optimize emissions performance before implementation. These tools improve auditing processes and identify emission reduction opportunities throughout production. Digital energy management systems optimize resource consumption, reduce your plant’s carbon footprint, and facilitate renewable energy integration. Digital technologies also support circular economy efforts by tracking material flows, verifying recycled feedstocks, and promoting closed-loop processes. Overall, digital solutions empower you to advance sustainability, meet regulatory standards, and achieve your environmental targets effectively.
Market Dynamics and Economic Impact of Industry 4.0 Adoption
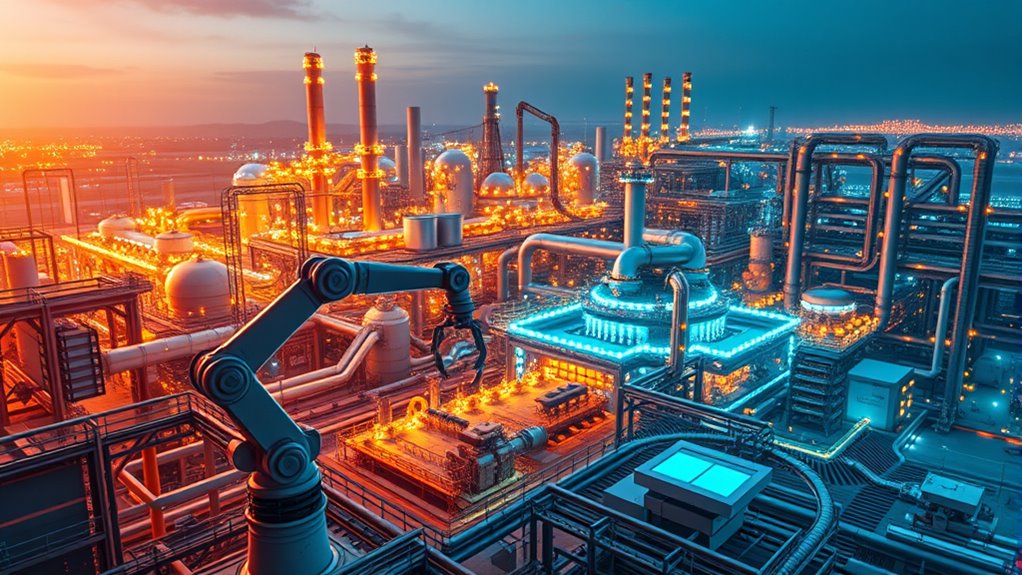
The adoption of Industry 4.0 technologies is transforming the chemical industry’s market landscape and driving significant economic shifts. The global Chemistry 4.0 market was valued at USD 63.91 billion in 2022 and is projected to reach USD 142.21 billion by 2031, with a CAGR of 9.53%. By 2024, it’s expected to grow to USD 87.52 billion, reaching USD 237.53 billion by 2034 at a 10.50% CAGR. This growth is fueled by increased use of AI and IoT, especially in the Asia Pacific region, driven by urbanization and manufacturing expansion. Digital transformation is also enhancing data-driven decision-making and operational agility across chemical plants. Industry 4.0’s integration boosts efficiency, enhances supply chain visibility, and supports employment in a sector with over 20 million jobs and $5 trillion in annual sales. These technological shifts generate ripple effects across related industries, amplifying their economic impact globally.
Addressing Challenges and Leveraging Digital Transformation Drivers
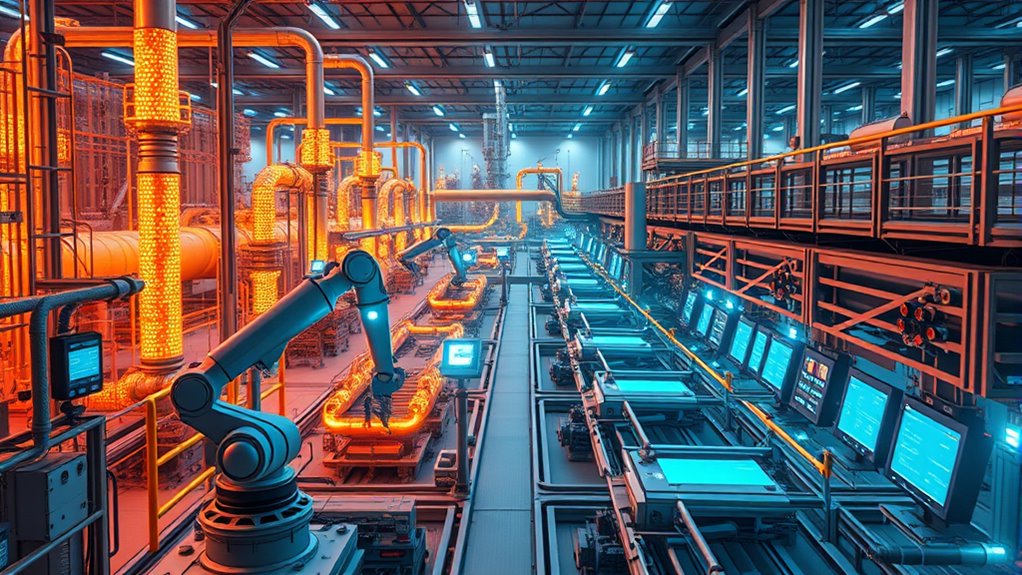
Steering the digital transformation of chemical plants involves overcoming a range of challenges that can hinder progress. Integration of diverse technologies and legacy equipment creates interoperability issues, while cybersecurity risks grow with increased connectivity, demanding stronger protections. Disparate standards and protocols complicate seamless implementation, and high upfront costs for new infrastructure can deter investment.
Managing vast data streams from sensors and automated systems requires specialized skills and platforms. Workforce barriers, such as talent shortages and resistance to change, slow adoption, emphasizing the need for comprehensive training. Organizational silos hinder collaboration, making alignment vital.
Additionally, evolving standards and strict regulatory requirements add complexity. Addressing these challenges involves strategic planning, adopting best practices, and leveraging enablers like IIoT and advanced analytics to access Industry 4.0’s full potential. Support hours for technical assistance, such as PlayStation support hours, can also influence operational downtime and planning in digital initiatives.
Case Studies of Successful Digital Integration in Chemical Plants
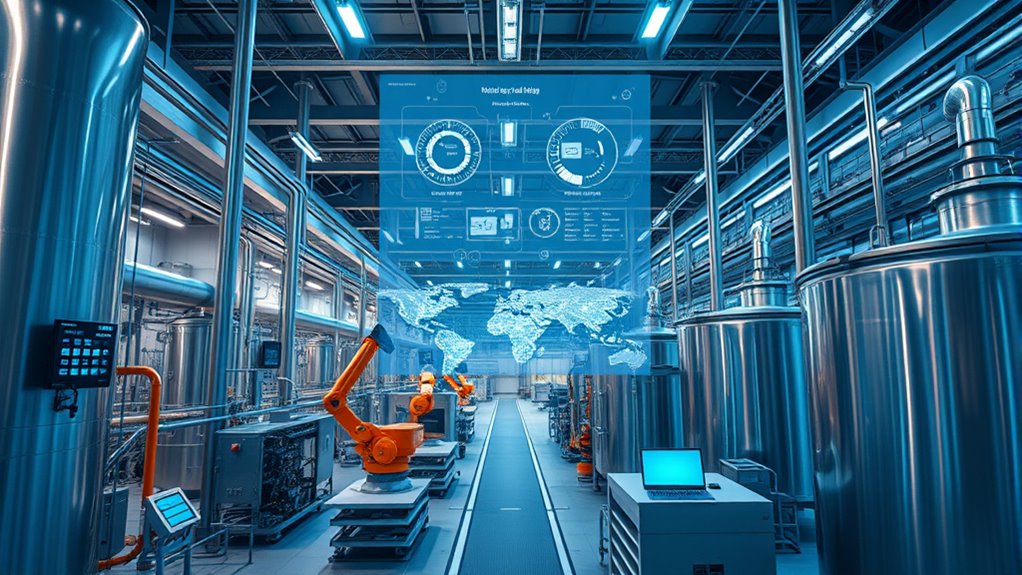
Successful digital integration in chemical plants demonstrates how advanced technologies can transform operations and improve performance. For example, IoT sensors enable real-time monitoring of critical equipment, reducing unexpected failures and downtime by up to 30%. Incorporating sound recording techniques can further enhance communication and data analysis within these systems, leading to more precise control and troubleshooting. Predictive maintenance powered by AI forecasts equipment degradation, saving 10-20% on maintenance costs and enhancing safety by detecting hazardous conditions early. Combining ERP and APS software provides complete visibility of production, allowing dynamic scheduling and a 15% increase in throughput. AI-driven quality control detects process deviations, cutting product defects by 40%. Digital twins and AI optimize energy use, reducing energy consumption and emissions by 10-15%. These case studies show how digital tools boost efficiency, safety, and sustainability, setting a strong foundation for ongoing industry transformation.
Future Outlook and Emerging Technologies in the Chemical Industry
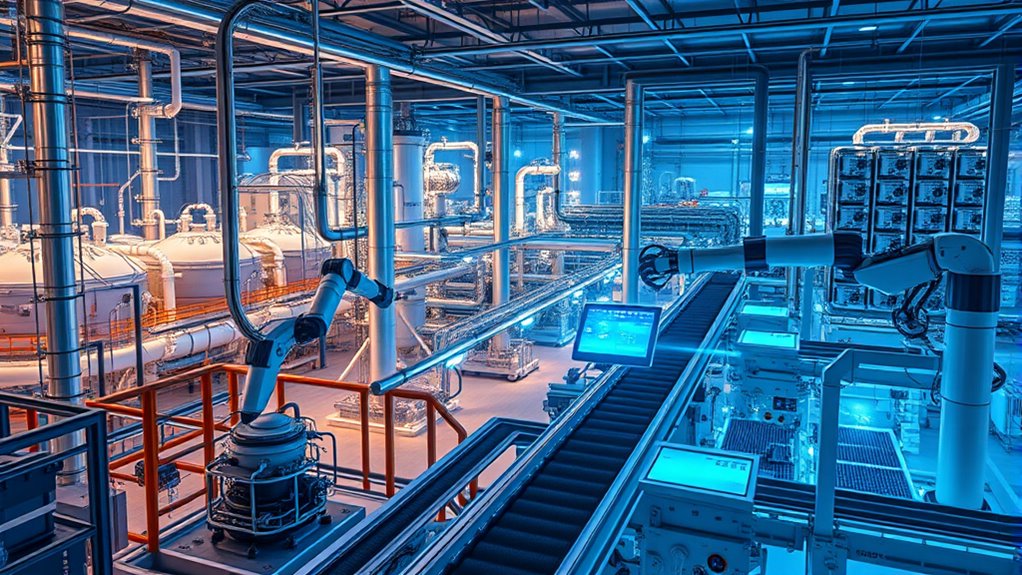
As the chemical industry advances toward a more sustainable and innovative future, embracing emerging technologies becomes essential for maintaining competitiveness. Digitalization and automation, like advanced sensors and robotics, will boost plant efficiency and safety.
Embracing digitalization and automation enhances efficiency, safety, and competitiveness in the evolving chemical industry.
AI and machine learning will enable predictive maintenance and process optimization, reducing downtime and costs. IoT integration will allow you to remotely monitor facilities, enhancing agility and responsiveness.
Developing new advanced materials will open doors to innovative applications across sectors. Blockchain will improve data security and supply chain transparency, building trust.
Long-term, these technologies will support sustainable practices and process innovations, helping you adapt to market challenges. By investing in R&D and forming strategic partnerships, you’ll position your operations for resilience, growth, and leadership in the evolving chemical landscape. Contrast ratio improvements in projectors can also enhance visual inspections and remote monitoring of plant environments.
Frequently Asked Questions
How Do Digital Tools Improve Safety in Chemical Manufacturing?
Digital tools improve safety in chemical manufacturing by enabling real-time monitoring, which helps you catch deviations early and respond quickly. They assist with accurate inventory management, reducing risks of misplaced chemicals.
Risk assessments become more thorough with software, and incident reporting improves safety responsiveness. Automation reduces human errors, and digital training resources enhance worker knowledge.
What Are the Key Barriers to Implementing Industry 4.0 in Chemical Plants?
You might think adopting new tech is easy, but the reality is a maze of barriers. You face a talent drought, with few skilled workers willing to join an industry seen as outdated. Costs skyrocket, and organizational resistance stalls progress.
Integrating complex systems and ensuring cybersecurity feels like fitting puzzle pieces that don’t quite match. These hurdles slow your digital journey, making transformation feel more like a distant dream than a near-future goal.
How Does Digital Transformation Impact Workforce Skills and Training Needs?
Digital transformation profoundly changes your workforce skills and training needs. You’ll need to develop digital literacy in data analytics, IoT, and AI, while bridging gaps between chemical engineering and new technologies.
Upskilling programs become essential, focusing on cloud computing, automation, and cybersecurity. You must also foster a culture of continuous learning and collaboration across departments, ensuring your team adapts quickly to technological changes and maintains operational excellence in increasingly digital environments.
What Are the Cost Implications of Adopting Industry 4.0 Technologies?
You might think adopting new technologies is too costly, but the cost implications actually offer significant savings. Initial investments in equipment and infrastructure are high, yet operational costs drop substantially over time thanks to automation, predictive maintenance, and energy efficiency.
These reductions can offset upfront expenses, boosting productivity and safety. While there’s a need for retraining and system upgrades, long-term benefits include enhanced competitiveness, lower maintenance costs, and improved plant resilience.
How Can Smaller Chemical Companies Compete With Larger Firms Through Digitalization?
You can compete with larger firms by leveraging digitalization through strategic partnerships, which give you access to advanced technologies and shared infrastructure. Invest in developing your team’s digital skills and foster a culture of continuous learning.
Use digital tools to improve efficiency, innovate faster, and enhance sustainability efforts. These steps help you stay agile, reduce costs, and respond quickly to market changes, giving you a competitive edge.
Conclusion
Embrace Industry 4.0 to transform your chemical plant through innovation, efficiency, and sustainability. Leverage advanced technologies to optimize operations, reduce costs, and enhance safety. Invest strategically to seize growth opportunities and stay competitive. Address challenges proactively and foster a culture of continuous improvement. By integrating digital solutions, you not only future-proof your business but also contribute to a greener, smarter, and more resilient chemical industry. The future is digital, and it’s yours to shape.