Chemical recycling breaks down plastics into basic chemicals like monomers and hydrocarbons, turning waste into valuable raw materials. Processes such as pyrolysis, gasification, and depolymerization use heat, catalysts, or chemicals to transform mixed or contaminated plastics efficiently. These methods help reduce landfill waste, lower emissions, and support a circular economy. To see how these technologies are advancing and shaping sustainable waste management, keep exploring the latest innovations in chemical recycling.
Key Takeaways
- Chemical recycling breaks plastics into basic chemicals like monomers, fuels, or syngas through processes such as depolymerization, pyrolysis, or gasification.
- Techniques involve thermal, catalytic, or enzymatic methods to decompose complex polymers into simpler, reusable chemical building blocks.
- Pyrolysis converts plastics into oils and gases, which can be refined into new plastics or chemicals.
- Gasification transforms plastics into syngas (carbon monoxide and hydrogen) for producing fuels or chemicals.
- These processes help recover valuable raw materials, reduce waste, and support a circular economy for plastics.
Understanding Chemical Recycling and Its Role in Waste Management
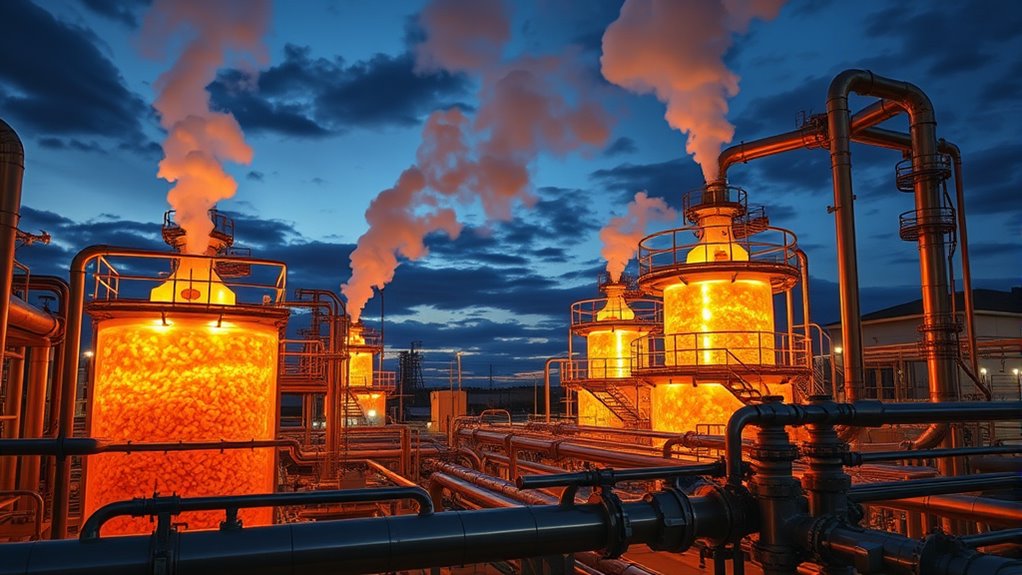
Have you ever wondered how waste plastic can be transformed into new materials? Chemical recycling changes the chemical structure of plastics, turning waste into raw materials like fuels, chemicals, or new plastic components. Unlike traditional methods, it preserves the quality of the original materials and can handle mixed or contaminated plastics that usually go unrecycled. This process helps reduce landfill and incineration waste, cutting emissions associated with waste disposal. Additionally, it can be integrated with expert advice to optimize recycling techniques and improve sustainability. However, it requires a lot of energy, which impacts its overall environmental benefits. Despite these challenges, chemical recycling is essential for a circular economy, recovering valuable resources and reducing dependence on virgin plastics. Advanced chemical recycling can process plastics that are not recyclable through mechanical methods, expanding recycling options. It offers a promising solution to manage plastic waste more sustainably and supports future waste management innovations.
Key Technologies Driving Chemical Breakdown of Plastics
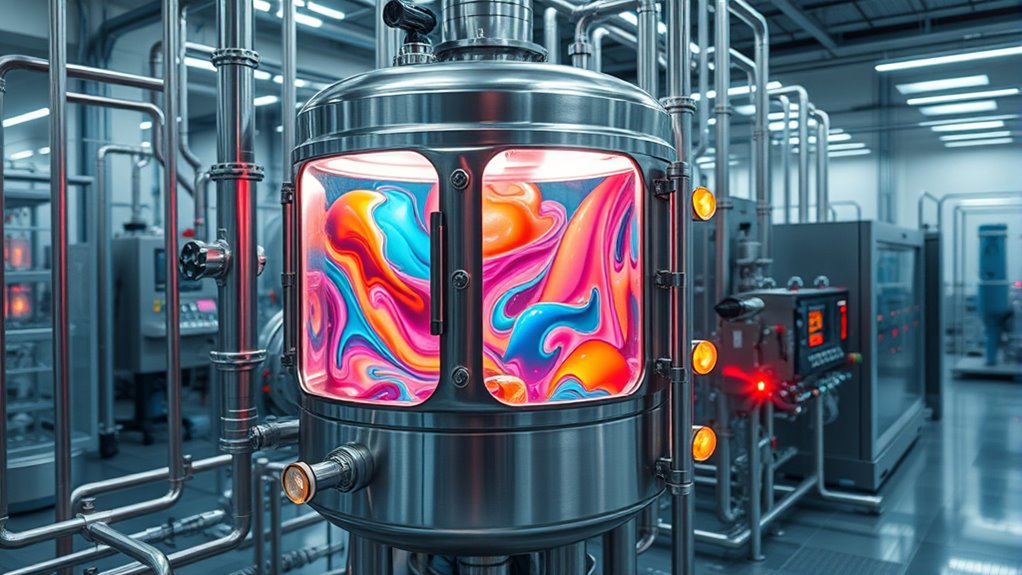
Advances in chemical recycling rely on a range of innovative technologies that enable the efficient breakdown of plastics into their fundamental components. Dissolution and purification techniques use solvents to selectively dissolve plastics, removing additives without altering the polymer structure, which allows for cleaner recycling streams. However, these methods are still mostly at a pilot stage and suited for specific feedstocks. These techniques can help recover plastics with complex formulations that are difficult to mechanically recycle. Depolymerization methods, including glycolysis, methanolysis, and enzymatic processes, break polymers like PET and nylon into monomers for reuse, supporting circularity. Enzymatic depolymerization is an emerging approach that offers promising eco-friendly solutions. Conversion processes beyond pyrolysis, such as gasification and hydrothermal treatment, transform plastics into fuels or chemicals with fewer byproducts. Catalytic and thermal innovations optimize reaction conditions, reduce energy use, and improve yields, making chemical breakdown more efficient and scalable.
Pyrolysis: Transforming Plastics Into Fuel and Chemicals
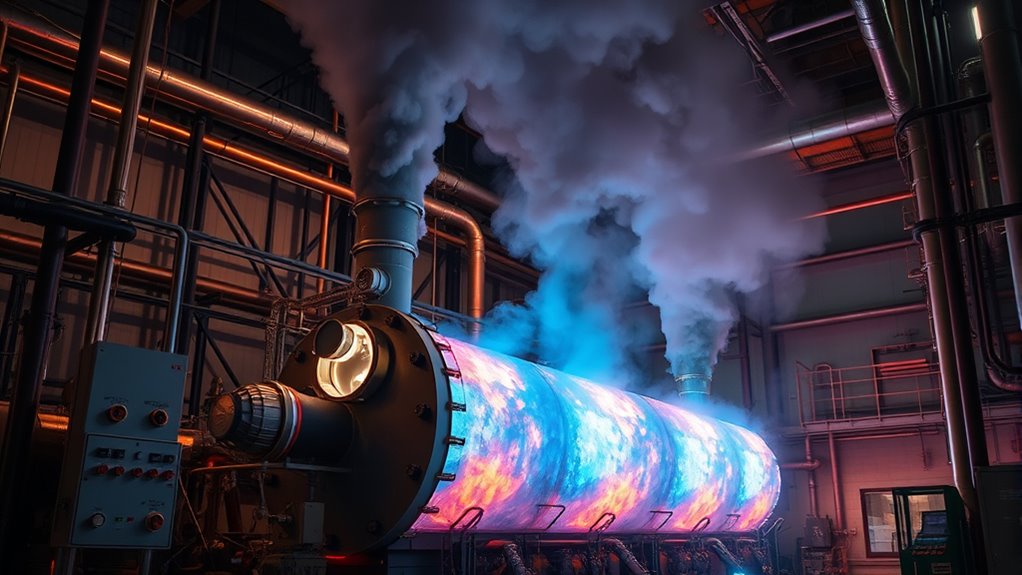
Pyrolysis offers a promising method for converting plastic waste into valuable fuels and chemicals by thermally decomposing polymers at around 500°C without oxygen. You vaporize plastic in a reactor, breaking it into smaller molecules. The process produces pyrolysis oil, fuel gas, char, and hydrocarbons. Pyrolysis oil can be refined into new plastics and chemicals, supporting circular recycling. Catalytic pyrolysis uses catalysts to speed up breakdown and improve product purity. Continuous methods like rotary kilns enable large-scale processing. This approach reduces landfill waste, recovers hydrocarbons, and creates valuable byproducts like char. However, energy use and emissions remain concerns. Overall, pyrolysis helps transform plastics into useful chemical feedstocks, advancing sustainable recycling efforts.
Product | Main Use | Key Benefit |
---|---|---|
Pyrolysis Oil | Feedstock for plastics, chemicals | Supports circular economy |
Char | Manufacturing additive | Waste reduction and value |
Gasification: Creating Syngas From Plastic Waste
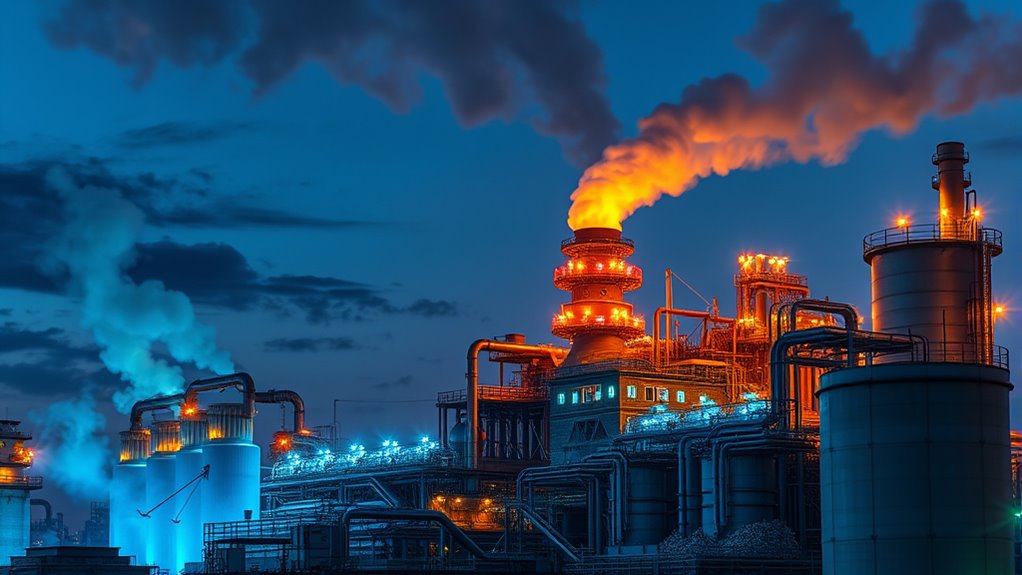
Did you know that gasification offers a promising way to convert plastic waste directly into useful energy and chemical sources? This thermochemical process transforms plastics into syngas, mainly composed of carbon monoxide and hydrogen, by heating them at high temperatures in a controlled environment. It can process various plastics, including contaminated and problematic types, without extensive pre-treatment. The resulting syngas resembles town gas and can replace natural gas for industrial heat or electricity generation. Gasification operates through stages like drying, pyrolysis, combustion, and reduction, using different reactor types to optimize efficiency. It also minimizes harmful emissions by binding halogens with lime. Additionally, advancements in power generation technologies are enhancing the efficiency and environmental benefits of gasification systems.
Depolymerization: Reclaiming Monomers for New Plastics
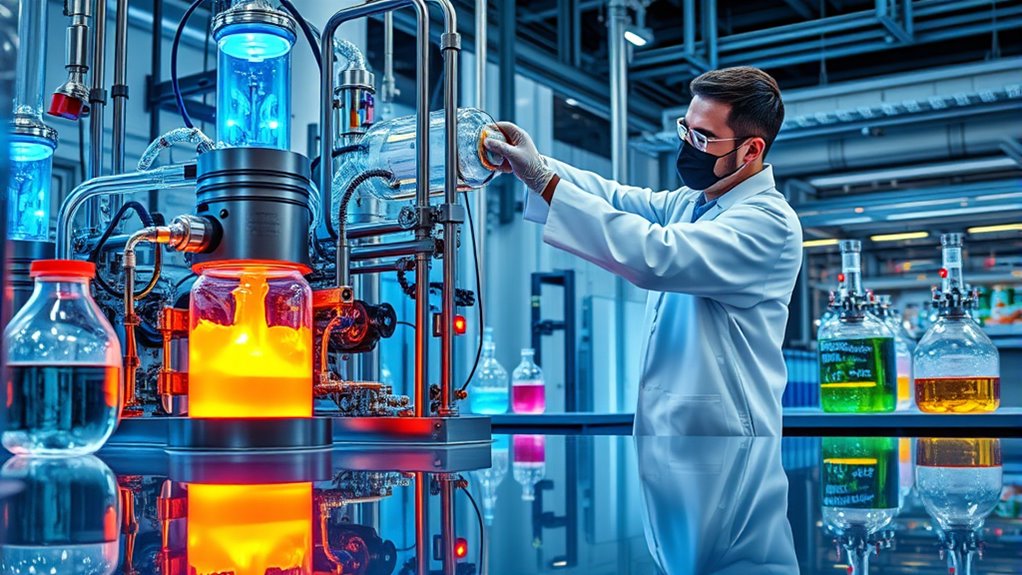
Have you ever wondered how plastic waste can be transformed back into its original building blocks? Depolymerization does just that by breaking down polymers into their monomers, enabling the production of new plastics.
The process involves sorting waste, then using solvents, heat, and catalysts to reverse polymerization. Techniques like methanolysis are common for PET, converting it into dimethyl terephthalate and ethylene glycol under high temperature and pressure. This step is crucial for ensuring that the feedstock is suitable for efficient chemical breakdown. Preparation of feedstock is essential to optimize the depolymerization process and maximize recovery rates, especially when dealing with complex or contaminated waste streams.
Purification removes contaminants, ensuring high-quality monomers suitable for reuse. While PET is the most advanced candidate, ongoing research aims to improve yields for plastics like polypropylene. Recycling processes are continually evolving to enhance efficiency and sustainability in chemical recycling. This method supports a circular economy by reclaiming monomers that match virgin materials in quality, reducing reliance on fossil fuels, and recycling complex or contaminated waste streams efficiently.
Advantages of Turning Plastics Back Into Basic Chemicals
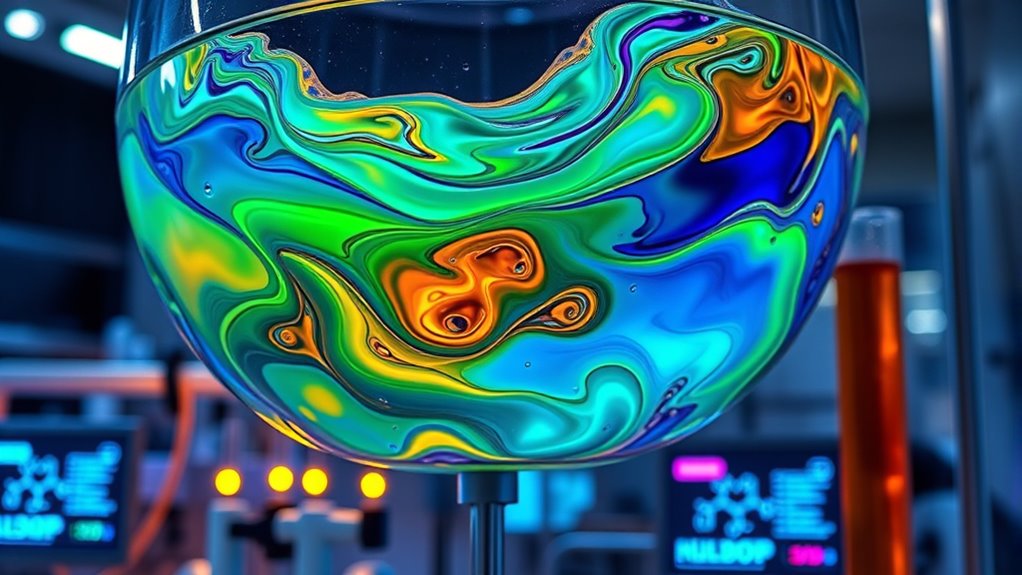
Turning plastics back into basic chemicals offers significant environmental and economic advantages. It reduces greenhouse gas emissions by at least 35%, with potential savings reaching 50-60% compared to incineration. This process also lessens reliance on fossil resources, cutting depletion by 35-75%, and sometimes even more. Furthermore, chemical recycling can contribute to a more sustainable and resilient supply chain by providing a stable source of high-quality raw materials. By replacing virgin feedstocks, you help lower the carbon footprint of plastic production and support climate change mitigation. Chemical recycling can process contaminated and mixed plastic waste, including polymers like PE, PP, and PVC, which mechanical methods struggle with. It enables the production of recycled plastics that match virgin quality, suitable for high-value uses like food packaging and auto parts. Advanced recycling technologies make this possible by breaking down plastics into basic chemicals at a molecular level. Ultimately, it reduces dependence on finite fossil fuels, promotes a circular economy, and conserves valuable resources for the future.
Overcoming Challenges in Chemical Recycling Processes
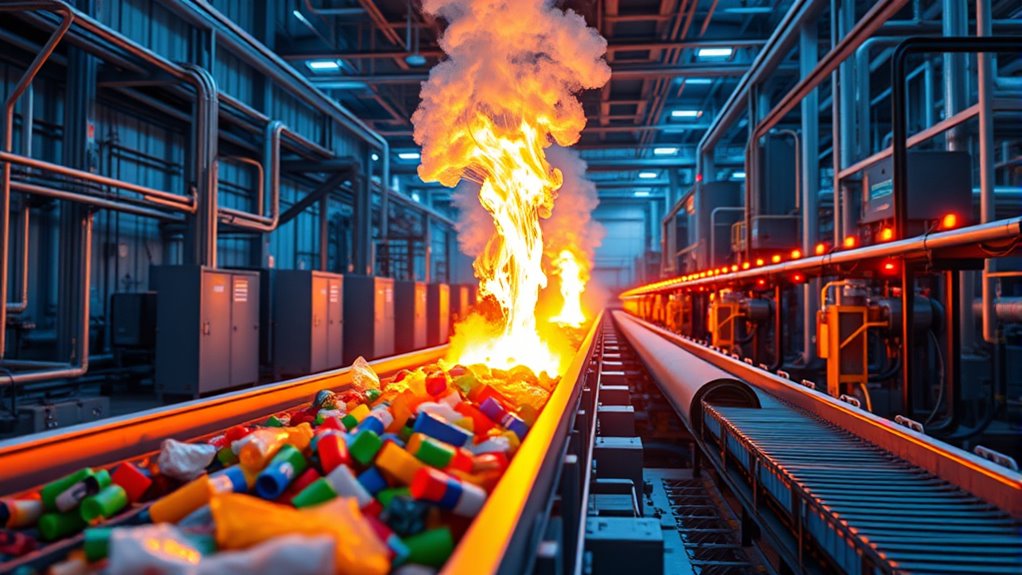
While chemical recycling offers promising environmental benefits, several technical challenges hinder its widespread adoption. Scalability remains a major hurdle, as current processes can’t handle the massive volume of global plastic waste.
The diversity of plastics complicates developing efficient methods, while high energy demands—often from non-renewable sources—add to costs. Expensive catalysts increase operational expenses, and ongoing research is essential to optimize yields and efficiency.
Environmental concerns also persist, with processes potentially releasing toxic emissions and contributing to greenhouse gases. High operating costs, fluctuating markets, and limited demand for recycled products threaten economic viability.
Additionally, a lack of standardized regulations and public skepticism slow progress. Overcoming these obstacles requires technological advancements, better process control, improved feedstock quality, and collaborative efforts across industries. Incorporating positive energy and maintaining a focused mindset can also drive innovative solutions to these challenges.
Industrial Uses and Growing Investments in Chemical Recycling
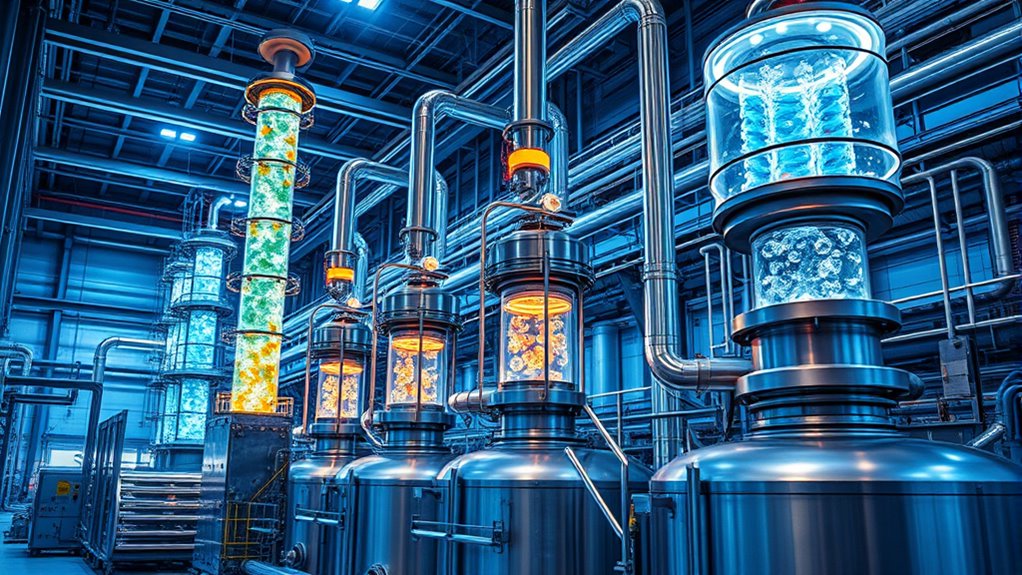
Industrial uses of chemical recycling are expanding rapidly as companies seek sustainable solutions for plastic waste. This technology produces high-quality recycled plastics, matching virgin materials, and is suitable for sensitive applications like food packaging. You’ll find chemically recycled plastics in products such as refrigerator parts, automotive dashboards, mattresses, carpets, and packaging. Processes like depolymerization and conversion create feedstocks for new plastics and chemicals within the petrochemical industry. These methods also handle mixed, contaminated waste streams that mechanical recycling can’t process, recovering valuable raw materials. As part of the circular economy, chemical recycling helps close the loop in manufacturing sectors. Somatic therapy techniques, while traditionally used in mental health, are also being explored to enhance worker well-being and stress management in industrial settings. Major companies and industry groups are investing in new plants to scale production, driven by regulations, sustainability commitments, and rising demand for circular plastics.
Environmental Benefits of Converting Plastics to Raw Materials
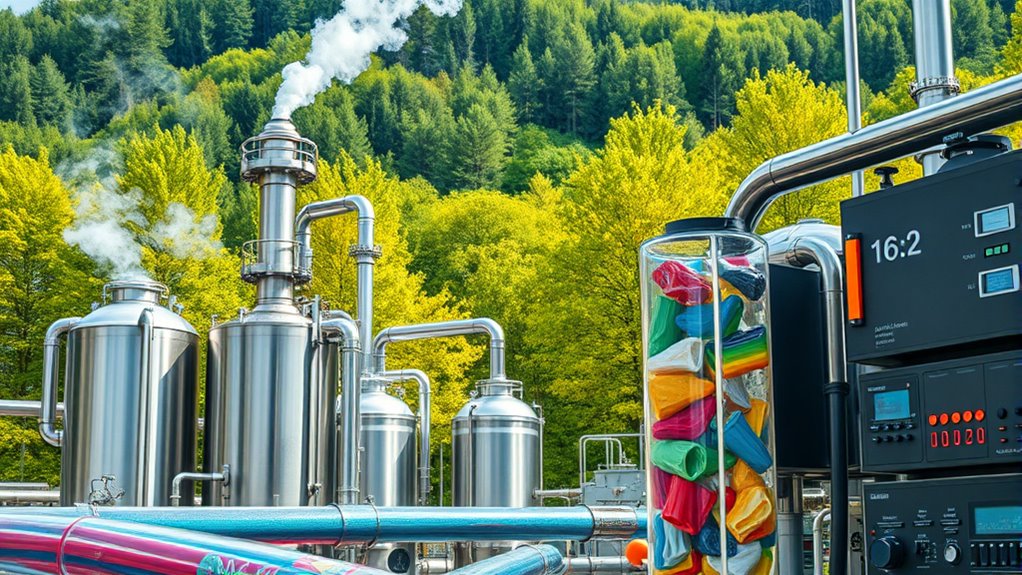
Converting plastics into raw materials through chemical recycling offers significant environmental advantages. It reduces greenhouse gas emissions by at least 50% and aims for 60% by 2030 compared to incineration. This process avoids emissions from fossil fuel extraction and traditional plastic production, lowering your carbon footprint.
It also conserves fossil resources—reducing depletion by up to 140% compared to incineration—by transforming waste into chemical feedstocks. Chemical recycling supports a circular economy, helping you divert plastics from landfills and incinerators, and promotes waste reduction.
Additionally, it produces high-quality raw materials suitable for demanding applications, matching virgin plastics in purity and safety. Enhancing sustainability through innovative recycling methods further minimizes environmental impact, conserves finite resources, and fosters a more sustainable plastic use.
Future Perspectives and Innovations in Chemical Recycling
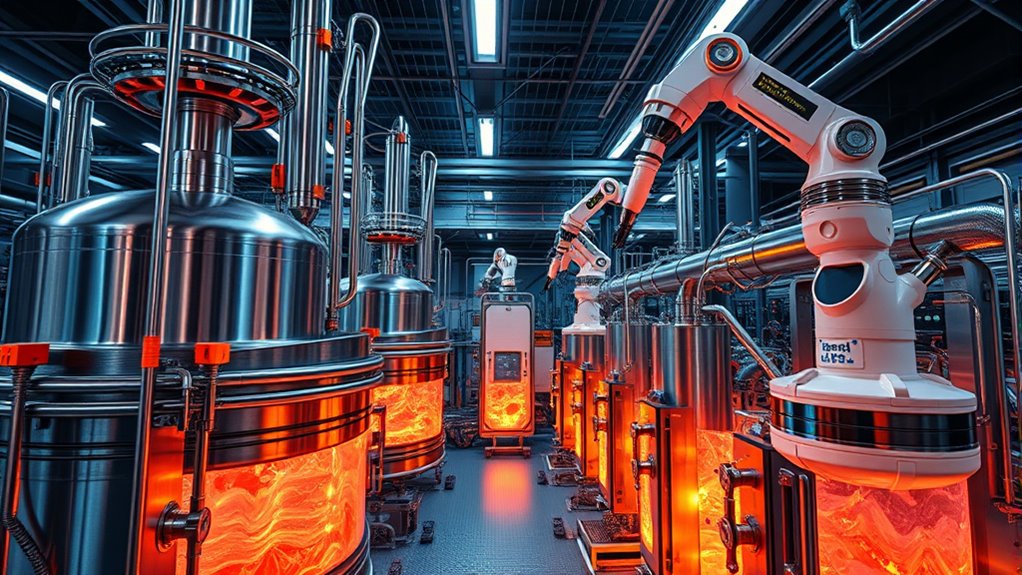
Advancements in chemical recycling are opening new possibilities for transforming plastic waste into high-quality raw materials. New technologies using heat, chemicals, or both target plastics that are difficult to recycle mechanically, boosting overall feasibility.
Researchers focus on maintaining polymer properties through multiple cycles, producing consistent feedstocks. Innovative catalytic and thermal processes aim to improve yield, purity, and energy efficiency, though scaling remains a challenge.
Significant investments, especially in Europe, are expected to expand infrastructure and global capacity, driven by policy support and industry commitment.
Chemical recycling’s ability to convert contaminated and mixed plastics into valuable feedstocks supports existing manufacturing and creates new products like fuels and specialty chemicals.
The development of headphone technology has also contributed to more efficient remote communication in industrial settings, enhancing safety and productivity.
These innovations promise a more sustainable, circular plastic economy by 2030, reducing reliance on virgin resources and lowering emissions.
Frequently Asked Questions
What Types of Plastics Are Most Suitable for Chemical Recycling?
You’re asking which plastics suit chemical recycling best. Condensation polymers like PET and polyamides work well with depolymerization, breaking back into original monomers for high-quality recycled plastics.
Addition polymers such as PE, PP, and PVC are suitable for pyrolysis, turning waste into basic chemicals or fuels. These methods handle contaminated or mixed plastics that mechanical recycling can’t process, helping reduce waste and boost recycling rates effectively.
How Energy-Intensive Are Chemical Recycling Processes Compared to Mechanical Recycling?
Think of chemical recycling as running a marathon in heavy gear—you’ll burn more energy than if you just took a brisk walk. It’s notably more energy-intensive than mechanical recycling because it involves high temperatures, pressures, and complex chemical reactions.
You’ll need extra energy for cleaning, sorting, and controlling reactions, making chemical recycling less efficient and more costly.
What Are the Potential Environmental Risks Associated With Chemical Recycling?
You should be aware that chemical recycling carries significant environmental risks. It can release toxic emissions like PAHs, VOCs, dioxins, and furans into the air, harming health and contributing to climate change.
Water pollution risks include hazardous wastewater and PCB contamination.
Land pollution occurs from hazardous waste and heavy metals.
Additionally, the lack of regulation and transparency increases the chance of environmental harm, especially if proper disposal and safety measures aren’t in place.
How Economically Viable Is Chemical Recycling at Large Industrial Scales?
You want to know if chemical recycling can be economically viable on a large scale. Right now, it’s costly, with expenses ranging from $300 to $1,000 per ton, compared to mechanical recycling.
But as facilities grow and technology improves, costs are expected to decrease.
High capital investments and lack of global standards pose challenges, yet government incentives and rising demand for recycled content could tip the balance toward viability.
Can Chemical Recycling Handle Multilayer or Heavily Contaminated Plastics Effectively?
You want to know if chemical recycling can effectively handle multilayer or heavily contaminated plastics. The good news is that new methods like STRAP have shown near-perfect efficiency in separating multiple polymers from multilayer films.
While contaminants pose challenges, ongoing research into less hazardous solvents and improved processes is promising. With continued innovation, chemical recycling is becoming more capable of managing complex and contaminated plastics effectively.
Conclusion
Chemical recycling offers a promising way to turn plastic waste back into valuable chemicals, helping reduce landfill overflow and pollution. Did you know that chemical recycling can process over 80% of plastics that traditional methods can’t? By embracing these technologies, you can contribute to a more sustainable future, transforming trash into raw materials for new products. It’s an exciting step toward a circular economy where plastics are reused instead of discarded.