You face growing cyber threats targeting chemical plants, from sophisticated nation-state attacks to vulnerabilities in outdated legacy systems. Attackers exploit weak points like unsecured remote access, inadequate network segmentation, and unpatched equipment, risking safety, operations, and profits. Implementing strong segmentation, regular patch management, and continuous monitoring helps reduce risks. Staying compliant with evolving regulations and integrating physical security enhances your defense. If you want to uncover more effective strategies, there’s much more to explore.
Key Takeaways
- Cyber threats target outdated OT systems via phishing, malware, and supply chain attacks, risking safety and production disruptions.
- Implement network segmentation, least privilege access, and multi-factor authentication to limit attack spread and enhance security.
- Regular patch management, vulnerability assessments, and continuous monitoring are essential for maintaining resilience.
- Leveraging IoT, AI, and advanced analytics improves real-time threat detection and predictive maintenance.
- Align cybersecurity practices with industry standards like ISA/IEC 62443 and maintain comprehensive risk management strategies.
The Evolving Cyber Threat Landscape in Chemical Facilities
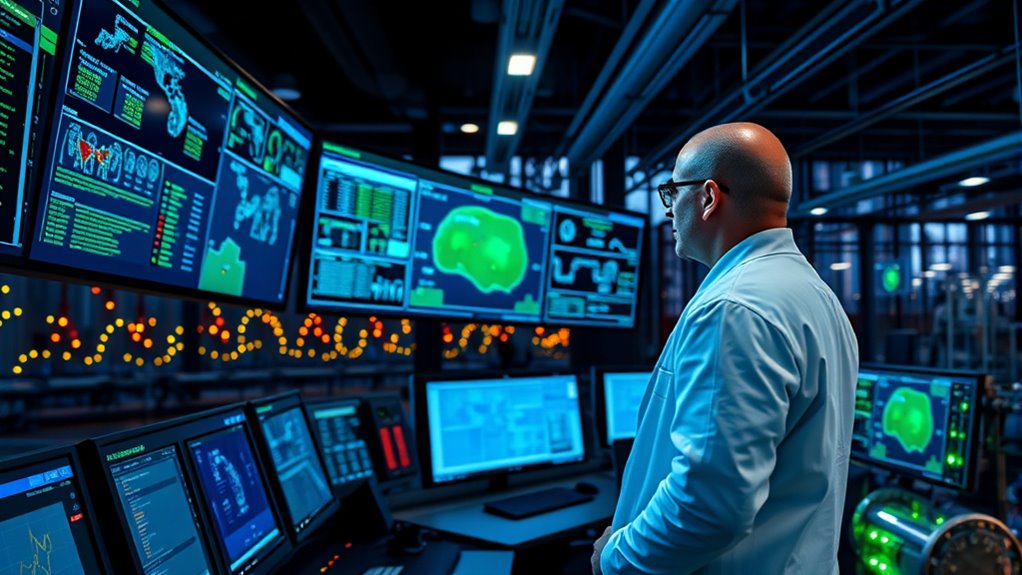
As cyber threats continue to evolve, chemical facilities face increasingly sophisticated and targeted attacks. State-backed groups, known as Advanced Persistent Threats (APTs), now target your operations for strategic and economic gains. Attack methods have grown more complex, involving phishing, exploiting public-facing applications, and supply chain compromises. Recent geopolitical tensions have escalated these risks, making your facility a more attractive target. The number of incidents is rising, and successful breaches can cause severe disruptions to production, supply chains, and safety. Increased connectivity, especially through remote access, heightens vulnerabilities in your systems. Cybercriminals focus on compromising critical infrastructure to steal data, disrupt operations, or cause physical hazards, emphasizing the urgent need for proactive cybersecurity measures in your chemical plant. The integration of high-tech equipment such as advanced sensors and control systems further expands the attack surface, necessitating comprehensive cybersecurity strategies. Moreover, the use of connected devices can introduce vulnerabilities in device security, which malicious actors may exploit to gain unauthorized access. Developing a comprehensive cybersecurity plan that considers the importance of attention and continuous monitoring can significantly reduce these risks.
Vulnerabilities Stemming From Legacy and Operational Technologies

Legacy and operational technologies in chemical facilities often present significant vulnerabilities because their age and design limit their security capabilities. Many OT systems are between 6 to 20 years old, lacking modern security features like user authentication and automatic updates.
These outdated systems often rely on unsupported hardware and software, making them susceptible to new threats. Incompatibility with modern security tools further hampers protection efforts. Because they’re designed without security in mind, OT systems are easy targets for targeted attacks and sabotage. Additionally, legacy systems often lack the ability to integrate with contemporary cybersecurity solutions, exacerbating their vulnerability. Recognizing the importance of vulnerability management is essential to address these risks effectively. Implementing comprehensive Kia Tuning strategies can help improve the resilience of control systems against evolving cyber threats.
Notable Cyberattack Techniques and Incident Examples
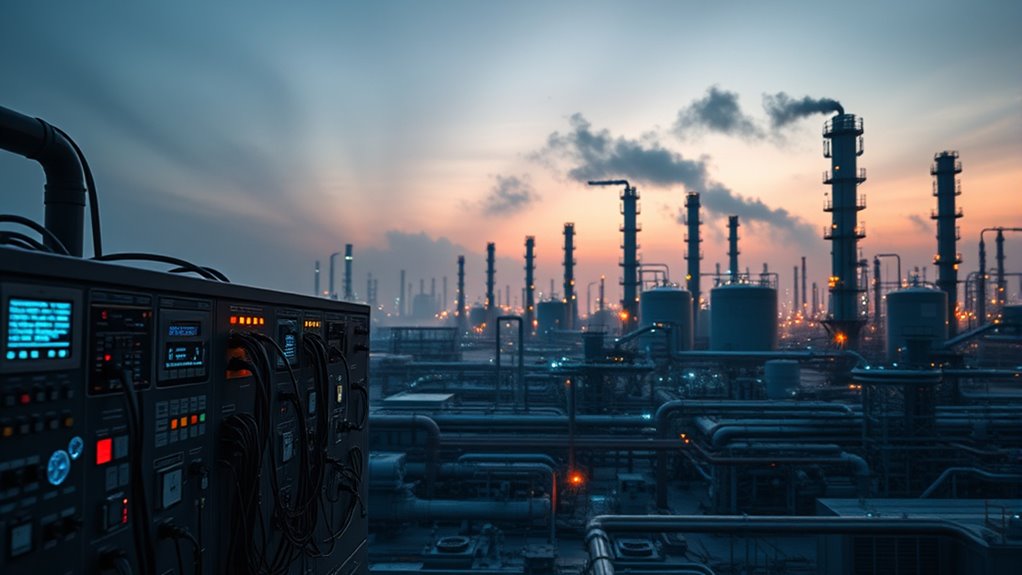
Cyberattack techniques targeting chemical plants have become increasingly sophisticated, exploiting vulnerabilities in outdated and insecure operational technologies. You may face malware designed to target specific OT systems, such as PLCs controlling critical processes, or attackers establishing long-term access through vulnerable entry points.
Exploiting bugs in widely used operating systems like Windows, as seen with Triton malware, can compromise safety systems, risking disaster. Attackers often manipulate PLCs to alter valve or pump operations, causing process disruptions or chemical spills. They might also push equipment beyond safety limits, risking catastrophic failures. Understanding cybersecurity vulnerabilities is crucial for implementing effective protective measures. Additionally, the integration of remote access into plant networks can expand attack surfaces if not properly secured, increasing the risk of intrusion. This highlights the importance of security protocols to safeguard critical infrastructure. Notable incidents include the 2017 Triton attack that targeted safety systems, and simulated exercises demonstrating how attackers could cause chemical spills by modifying PLC settings. These techniques highlight the growing threats to plant safety and operational integrity.
Implementing Effective Network Segmentation and Access Controls
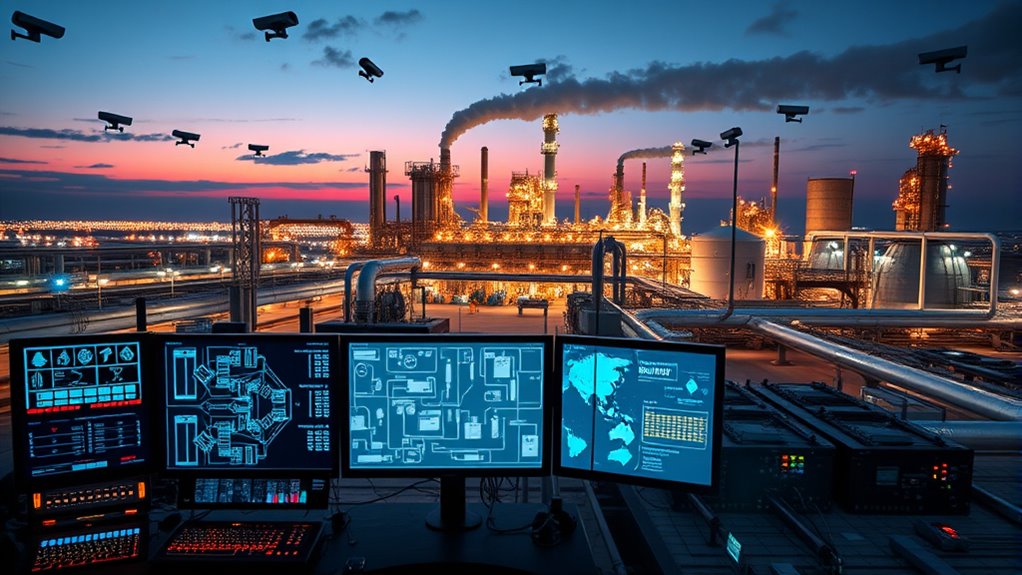
Implementing effective network segmentation and access controls is essential for safeguarding chemical plants against cyber threats. You should divide OT environments into isolated zones, limiting the spread of attacks and protecting critical assets.
Tailor security controls for each zone, balancing protection for sensitive systems with flexible access for less critical areas to maintain efficiency.
Use advanced techniques like Layer 2.5 segmentation and Zero Trust architectures beyond traditional VLANs, deploying dedicated firewalls and secure zones for external connections.
Enforce strict access controls based on least privilege, employing multi-factor authentication and VPNs for remote access.
Regularly audit permissions and monitor network traffic to detect abnormal activity.
Additionally, staying informed about breakthroughs in cybersecurity can help organizations adapt their defenses to emerging threats.
Combining segmentation with robust access controls helps contain incidents, improves detection, and ensures operational resilience against evolving cyber threats.
The Role of Regular Updates and Patch Management

Regular updates and patch management play an essential role in maintaining the security of industrial control systems (ICS) and operational technology (OT) environments. They address vulnerabilities that hackers could exploit, reducing the risk of cyberattacks.
To be effective, patch management involves identifying, sourcing, testing, deploying, and documenting patches, ensuring they’re approved by OEMs before deployment.
In OT environments, patching can be more complex due to specialized equipment and limited resources, making traditional methods less effective.
Regular updates also help you stay compliant with regulatory standards and prevent security breaches.
By maintaining an ongoing patching process, you improve your system’s security posture, minimize downtime, and protect critical operations from cyber threats.
Consistent patch management is crucial for safeguarding your plant’s safety and productivity.
Enhancing Detection and Response Through Monitoring and Training
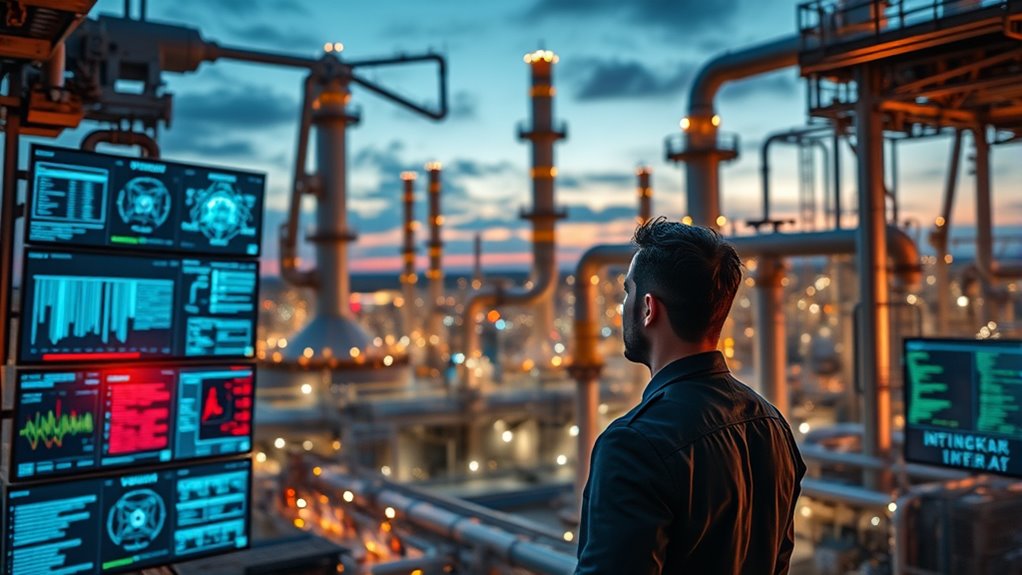
Enhancing detection and response in a chemical plant requires a proactive approach to monitoring and training. You should implement Intrusion Detection and Prevention Systems (IDPS) to monitor network traffic in real-time, spotting suspicious activity early.
Use network segmentation, firewalls, and DMZs to control traffic flow, reducing vulnerabilities and making anomaly detection easier.
Employ SIEM tools to analyze logs from various sources, speeding up incident identification.
Regularly monitor ICS and SCADA networks, isolating them from external threats.
Develop detailed incident response plans, conducting tabletop exercises and drills to identify gaps.
Provide ongoing cybersecurity training tailored to OT staff, emphasizing threat recognition and secure operations.
Promoting vigilance and scenario-based training enhances your team’s ability to respond swiftly and effectively to cyber incidents.
Navigating Regulatory Challenges and Ensuring Compliance
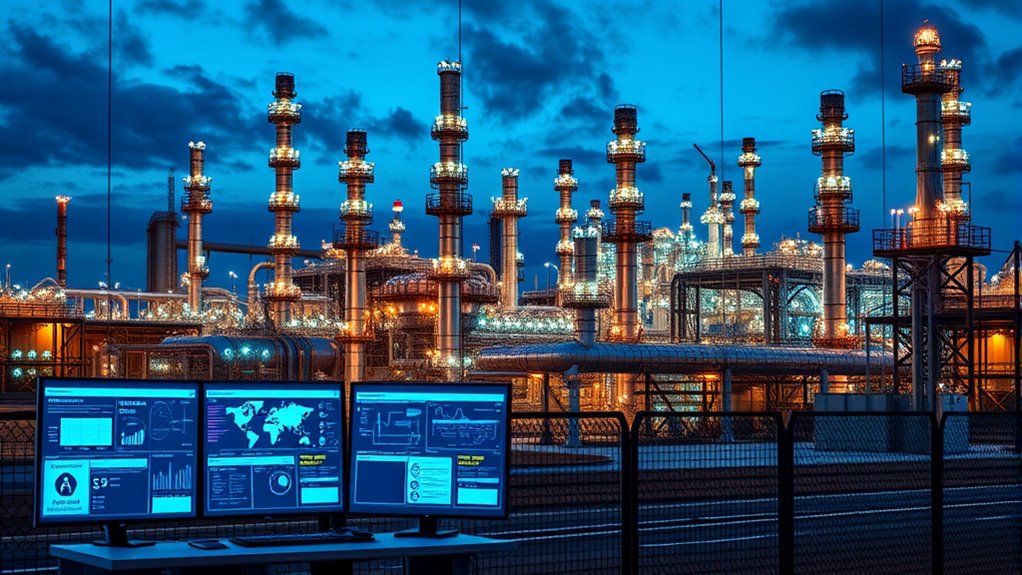
Managing regulatory challenges in a chemical plant requires a clear understanding of evolving standards and proactive compliance strategies. You need to stay updated on frameworks like ISA 62443, which guides cybersecurity management systems, and CFATS, though outdated, still influences physical and cyber security protocols.
Legislative developments are continuously shaping policies to address new threats, so aligning with international standards helps guarantee global compliance. To stay on track, maintain detailed inventories of OT devices and conduct regular audits to identify gaps.
Prioritize risks based on assessments and document all processes thoroughly for reporting. Engaging stakeholders and working closely with regulatory bodies is essential. By staying informed and organized, you can navigate complex regulations and ensure your plant remains compliant and resilient against cyber threats.
Leveraging Emerging Technologies for Improved Security
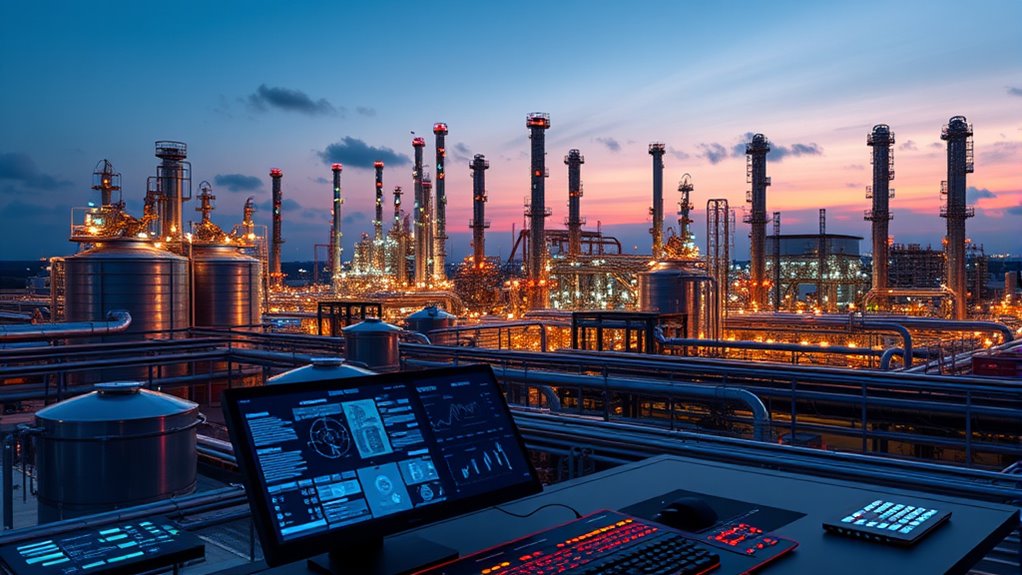
In today’s evolving threat landscape, leveraging emerging technologies like IoT and AI can substantially boost your chemical plant’s security posture. IoT devices enable real-time monitoring of operations, giving you better visibility into potential security threats.
AI and machine learning analyze data from these devices to predict and prevent cyber attacks before they escalate. Network segmentation, supported by IoT and AI, helps limit an attacker’s access and contain breaches.
Advanced OT network monitoring tools provide detailed insights into vulnerabilities, allowing you to address weaknesses proactively. Additionally, integrating IoT and AI into predictive maintenance reduces downtime and improves operational reliability.
Integrating Cybersecurity With Physical Security and Safety Protocols
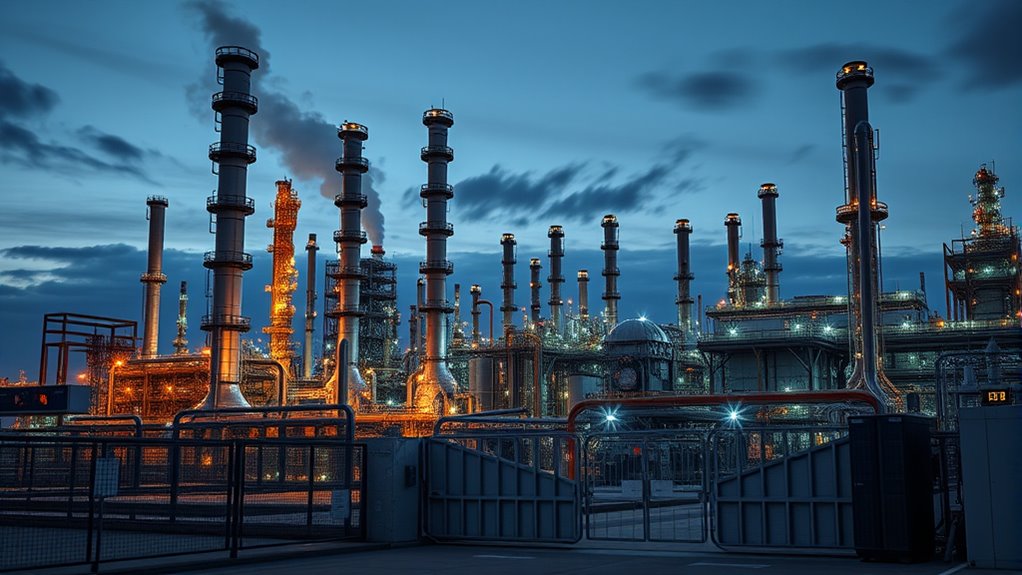
Integrating cybersecurity with physical security and safety protocols creates a holistic defense that addresses both digital and physical threats simultaneously. This approach ensures thorough protection by combining layered security measures like remote video surveillance, access controls, and cybersecurity defenses aligned with CFATS guidelines.
Integrating cybersecurity with physical safety creates comprehensive protection against digital and physical threats.
Developing risk management plans helps identify vulnerabilities across systems and ensures compliance with evolving standards. Physical incidents can be exploited to access cyber systems, so addressing both aspects together prevents cascading effects.
By unifying threat mitigation efforts, you enhance safety and reduce vulnerabilities. Continuous monitoring, employee training, and regular security audits are essential to maintain this integrated defense.
When you synchronize these protocols, you create a resilient environment that effectively counters complex, converging threats to your chemical plant.
Frequently Asked Questions
How Can Chemical Plants Effectively Assess Their Cybersecurity Risk Levels?
You can effectively assess your cybersecurity risk levels by conducting multidisciplinary workshops tailored to your plant’s operations. Use guidewords to identify vulnerabilities in critical systems like SCADA and ICS, and incorporate these findings into your hazard analysis.
Regularly update software, enforce strict access controls, and monitor systems continuously.
Engage third-party experts for impartial assessments and guarantee compliance with industry standards like CFATS and Risk-Based Performance Standards.
What Are the Most Common Indicators of a Cyber Breach in Chemical Facilities?
Imagine waking up to chaos—unusual network activity, unexplained system downtimes, or data suddenly changing. These are your biggest warning signs of a breach in your chemical plant.
You might also see unauthorized access attempts or security alerts blaring like sirens. These indicators scream that someone’s sneaking in, risking safety, operations, and your reputation.
Stay vigilant, monitor closely, and act fast to keep your facility safe from disaster.
How Do Supply Chain Vulnerabilities Impact Chemical Plant Cybersecurity?
Supply chain vulnerabilities directly impact your plant’s cybersecurity by introducing compromised software and hardware that attackers can exploit. When third-party suppliers or contractors have weak security, they can serve as entry points for threats.
This gives hackers remote access or enables malware infections. This interconnected risk means you must scrutinize suppliers, implement rigorous testing, and enforce security measures throughout your supply chain to protect your operations effectively.
What Role Does Employee Training Play in Preventing Cyber Incidents?
You play a crucial role in safeguarding your facility by staying informed and vigilant. Proper training helps you recognize subtle signs of cyber risks and insider threats, empowering you to act swiftly.
How Can Chemical Plants Prepare for Emerging Cyber Threats and Attack Methods?
You can prepare for emerging cyber threats by staying informed on the latest attack methods and vulnerabilities. Regularly update your security protocols, implement industry best practices like NIST or ISA/IEC standards, and adopt advanced detection tools such as anomaly detection systems.
Strengthen your network segmentation, ensure strong access controls, and conduct continuous vulnerability assessments.
Also, foster a security-aware culture through ongoing training, so everyone recognizes and responds effectively to new threats.
Conclusion
Staying ahead in chemical plant cybersecurity means continuously adapting to threats, much like a knight guarding their castle. You must implement best practices, from network segmentation to regular updates, and stay vigilant with monitoring and training. Remember, complacency is your enemy—cyber threats evolve faster than a medieval siege engine. Embrace emerging technologies and integrate security into every layer of your operations to protect both people and assets effectively.