Green hydrogen offers the chemical industry a clean, sustainable alternative to traditional methods, reducing carbon emissions and supporting decarbonization goals. Produced using renewable energy through advanced electrolysis, it can replace fossil fuels in processes like ammonia, methanol, and refining, while emitting only water vapor. As technological advances lower costs and infrastructure improves, green hydrogen is poised to transform industry operations. To learn how this shift can impact your sector, explore the benefits and challenges further.
Key Takeaways
- Green hydrogen offers a zero-emission alternative for chemical manufacturing, reducing carbon footprints in processes like ammonia and methanol production.
- It enables existing infrastructure to be adapted with minimal modifications for cleaner, sustainable chemical synthesis.
- The use of green hydrogen enhances industry decarbonization efforts, supporting global climate targets and policy initiatives.
- Technological advancements in electrolysis and renewable energy integration are lowering costs, making green hydrogen more viable.
- Challenges remain in scaling infrastructure and reducing costs, but future innovations promise broader adoption in the chemical sector.
The Growing Role of Hydrogen in Chemical Manufacturing
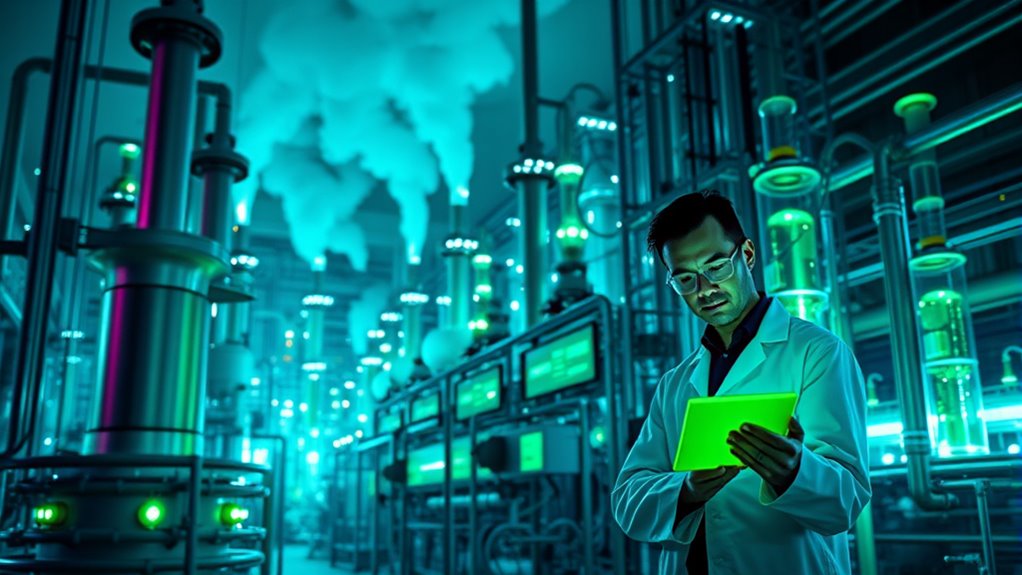
Hydrogen is becoming increasingly crucial in chemical manufacturing, primarily serving as a key feedstock for producing ammonia, methanol, and refined fuels. You should know that around 45 million metric tons are used globally each year, making up 40% of total hydrogen consumption in the industry. The shift toward low-carbon hydrogen, especially electrolytic hydrogen from renewable sources, is transforming processes like ammonia synthesis, where existing infrastructure can often be adapted with minimal changes. While cost remains a hurdle, scalable green hydrogen is essential for reducing carbon footprints. Additionally, hydrogen’s role extends into hydrogenation processes, refining, and producing specialty chemicals. As you explore sustainable solutions, understanding hydrogen’s foundational role in these manufacturing processes highlights its importance for a cleaner, more efficient chemical industry. Hydrogen’s widespread use in industry underscores its critical position in current and future chemical manufacturing. Moreover, advancements in renewable energy integration are expected to further lower costs and increase hydrogen availability.
Environmental Benefits of Transitioning to Green Hydrogen
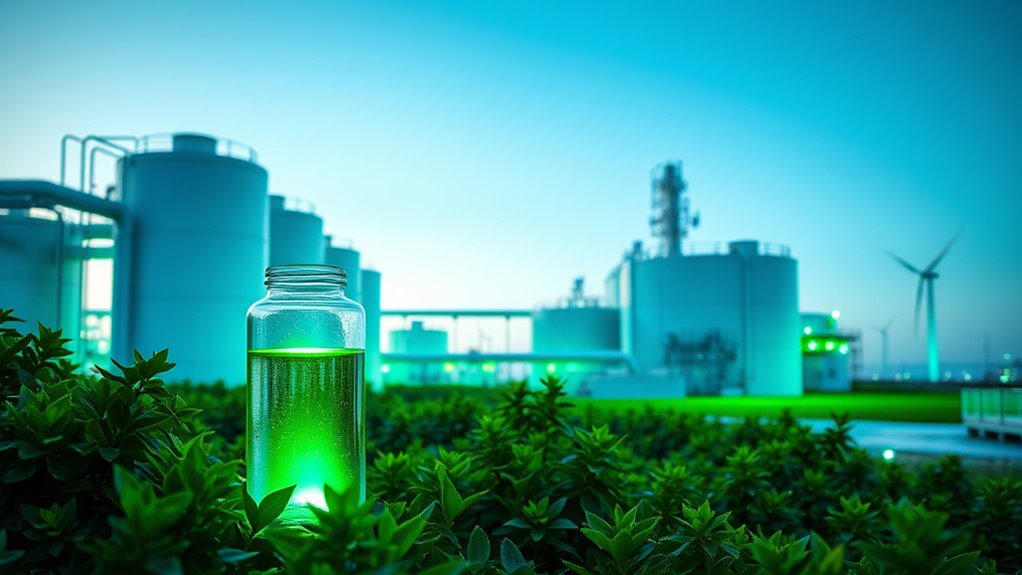
Have you ever considered how switching to green hydrogen can dramatically cut greenhouse gas emissions? Because it’s produced using renewable electricity, green hydrogen emits no CO₂ during production or use. When burned, it releases only water vapor, helping to fight climate change. Green hydrogen can generate heat up to 3812°F, making it suitable for high-temperature industrial processes that are difficult to electrify. This makes it a key decarbonization tool for industries that are hard to electrify, including chemical manufacturing. Moving forward reduces carbon footprints and supports global efforts toward carbon neutrality. Plus, green hydrogen improves air quality since hydrogen fuel cells emit only water vapor, avoiding pollutants like nitrogen oxides and particulate matter. Its use cuts harmful emissions at the source, benefiting public health and helping industries meet stricter environmental regulations. Additionally, understanding cybersecurity vulnerabilities associated with industrial control systems is essential as the industry adopts new green technologies.
Technological Advances and Production Methods
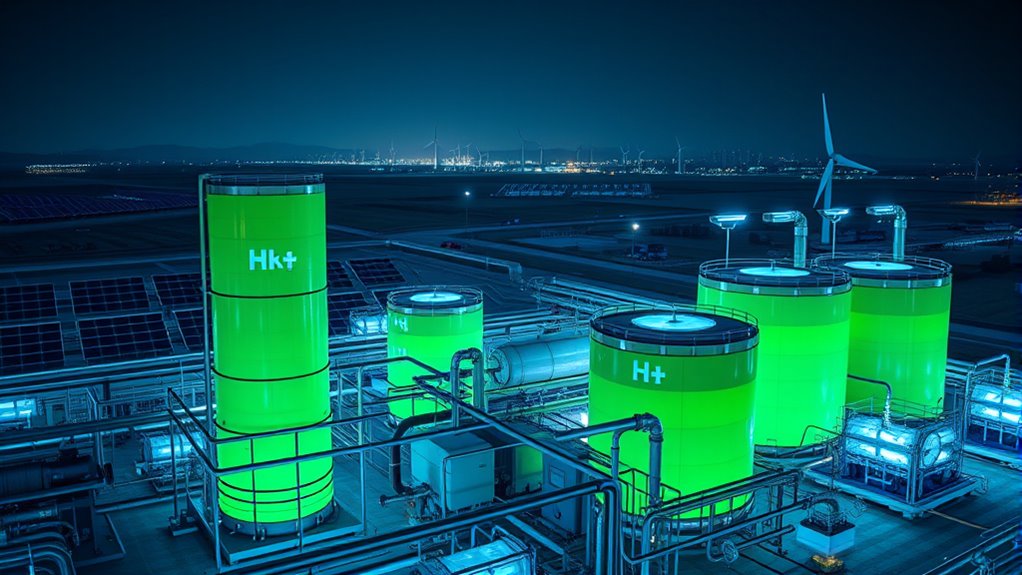
Recent innovations in electrolysis technology are revolutionizing green hydrogen production, making it more efficient and cost-effective. Advanced electrolyzer designs, like PEM and alkaline systems, now achieve efficiencies over 80% with renewable energy. Produced using renewable energy sources only, ensuring zero carbon emissions. High-temperature solid oxide electrolyzers are emerging, using excess industrial heat to cut energy demands. Dynamic load operation allows electrolyzers to adapt to intermittent renewables, supporting grid stability. Cost reductions aim for electrolyzers below $400 per kilowatt by 2030, driven by new materials. Researchers are also developing direct seawater electrolysis, addressing freshwater shortages with membrane-based desalination. Solar-driven methods, such as PEC cells and solar thermochemical cycles, directly convert sunlight into hydrogen, increasing efficiency. Hybrid PV-electrolysis systems and artificial photosynthesis are further advancing solar-to-hydrogen conversion, expanding production possibilities.
Key Applications Driving Decarbonization
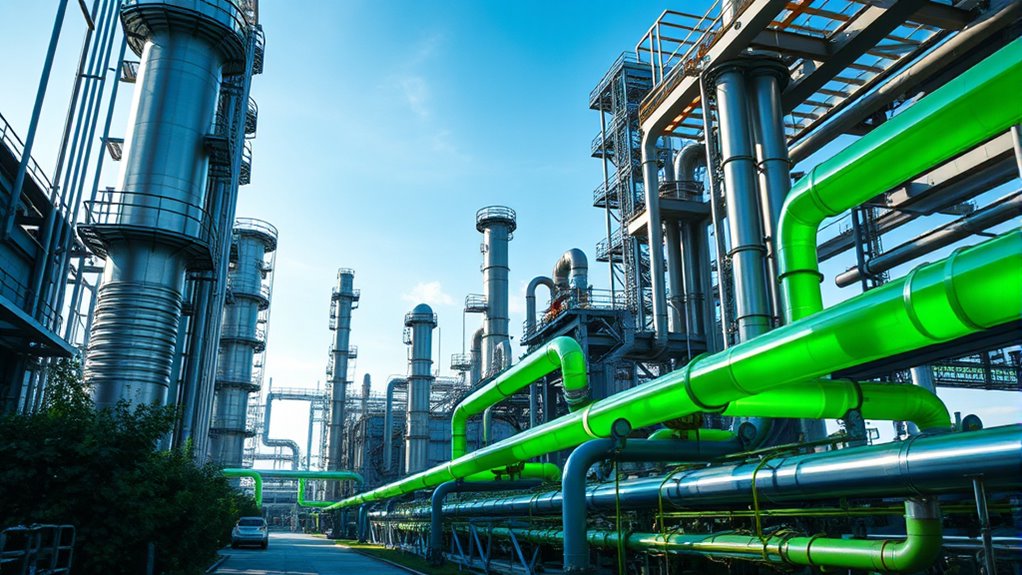
Green hydrogen plays a pivotal role in driving decarbonization across various industries, particularly in chemical manufacturing. You can use it in ammonia production, replacing fossil fuels and dramatically reducing emissions.
In methanol synthesis, green hydrogen offers a cleaner alternative, lowering the carbon footprint of chemical feedstocks. Hydrogenation processes across multiple chemical reactions become more sustainable with green hydrogen, cutting emissions and improving efficiency.
It’s also transforming petrochemical refining by reducing environmental impacts. These applications not only lower carbon footprints but also enhance energy efficiency, making industries more sustainable.
Governments support these shifts through policies and projects like the EU’s H2Glass, encouraging global adoption. As green hydrogen integrates into these key applications, it accelerates industry-wide decarbonization and supports a cleaner, more sustainable chemical sector.
Overcoming Challenges and Shaping the Future of Hydrogen Use
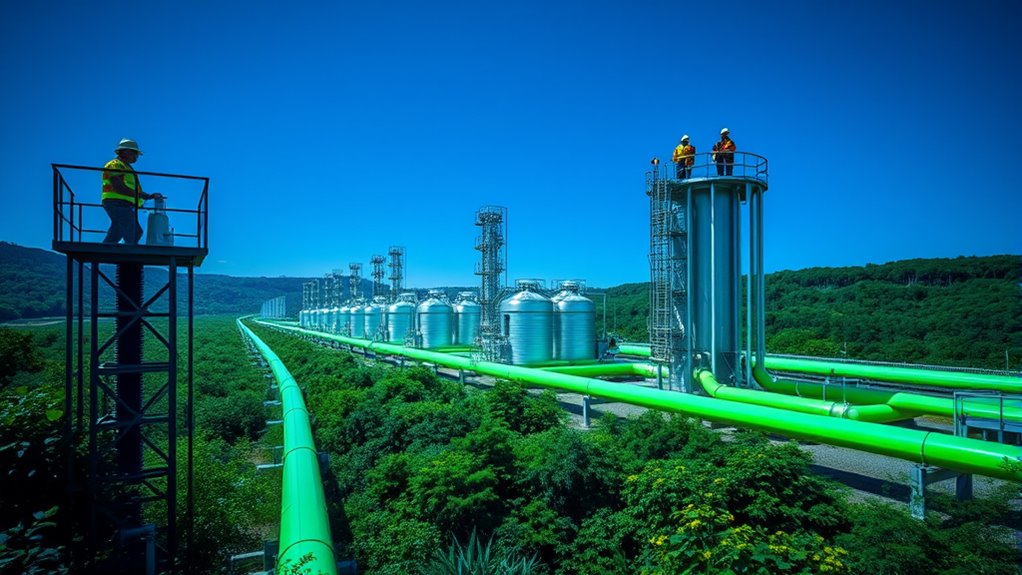
While green hydrogen offers promising applications for decarbonizing industries, several obstacles must be addressed to unlock its full potential. You’ll need to navigate energy and infrastructure constraints, as green hydrogen production demands vast renewable energy resources, competing with other sectors.
Scaling up capacity requires developing infrastructure for storage and transportation, especially for industries relying on on-site grey hydrogen. Cost remains a hurdle, with green hydrogen still more expensive than grey due to high renewable and electrolysis costs.
Advancements in technology, economies of scale, and policy incentives can help close this gap. The chemical industry, already familiar with hydrogen handling, can adapt existing facilities for green hydrogen use.
Strong regulation, market demand, and cross-sector collaboration are essential to overcoming these challenges and shaping a sustainable hydrogen future. Maximizing space and organization can also play a role in efficiently managing the storage and handling of hydrogen supplies, ensuring safety and operational effectiveness.
Frequently Asked Questions
How Cost-Effective Is Green Hydrogen Compared to Traditional Fossil-Based Hydrogen?
You might wonder how green hydrogen compares to fossil-based hydrogen regarding cost. Currently, green hydrogen is considerably more expensive, costing about $6.14 per kilogram versus $1.80 for natural gas–based hydrogen.
However, by 2030, costs could drop as technology improves and renewable energy becomes cheaper. With policy support and economies of scale, green hydrogen may become competitive, especially in climate-conscious markets.
What Policies Are Supporting the Adoption of Green Hydrogen in the Chemical Industry?
You’ll find that policies supporting green hydrogen adoption focus on integrating renewable energy, offering economic incentives, and creating regulatory frameworks that reduce emissions.
Governments also back industry-specific support and R&D to improve technology and infrastructure. These policies aim to make green hydrogen more affordable and scalable, helping the chemical industry shift away from fossil fuels, cut emissions, and stay competitive in a growing market focused on sustainability and innovation.
How Scalable Are Current Green Hydrogen Production Technologies for Large Chemical Plants?
The current question isn’t a walk in the park, but your options are promising. You can start small with modular electrolyzers that grow as needed, and AI optimization boosts efficiency.
Decentralized systems and innovations like membrane-free electrolysis simplify scaling. While costs and infrastructure pose hurdles, government support and regional projects help bridge gaps.
With ongoing tech advancements, scaling up for large chemical plants is becoming less of a leap and more of a calculated step forward.
What Are the Safety Considerations When Integrating Hydrogen Into Chemical Manufacturing?
When you integrate hydrogen into chemical manufacturing, safety becomes a top priority. You need to manage electrical hazards from electrolysis, prevent hydrogen leaks, and control flammability risks.
Use proper materials resistant to embrittlement and implement leak detection systems. Develop extensive safety protocols, conduct thorough risk assessments, and ensure compliance with regulations.
Educate your team and prepare emergency response plans to protect workers, the environment, and your operations from potential hazards.
How Does Green Hydrogen Impact the Overall Lifecycle Emissions of Chemical Products?
You want to know how green hydrogen affects the total lifecycle emissions of chemical products. By replacing traditional hydrogen with green hydrogen, you considerably cut emissions from production, especially for chemicals like ammonia and methanol.
Using renewable energy for electrolysis makes green hydrogen cleaner, reducing embedded emissions and lowering your product’s carbon footprint.
As technology advances and costs decrease, you’ll find green hydrogen becomes a more sustainable, eco-friendly option for your chemical processes.
Conclusion
Imagine your chemical plant as a ship steering toward a greener horizon, with green hydrogen as your guiding star. As you embrace this clean energy, you’ll navigate through stormy waters of climate change and regulatory pressure, steering toward sustainability. With breakthroughs in technology and increasing demand, green hydrogen is the wind filling your sails. Together, you can transform the industry, charting a course toward a cleaner, more resilient future that benefits both your business and the planet.